COMFORT OF AN UNDERFLOOR HEATING
In general there are three kinds of heat transfer - conduction, convection and radiation.
With an underfloor heating the heat is transmitted through radiation. This has the advantage that all room confining areas show a homogenous temperature allocation.
The use of an underfloor heating also avoids the raise of dust as known from radiator heatings and this way improves the room hygiene. Since dust often causes allergies, a panel heating can create a healthier surrounding. In general the room shows less hot and dry air due to the even heat distribution. The respiratory system of the residents is less irritated and the risk of inflammations and the growth of bacteria and viruses is minimised.
Furthermore, there are no humid zones on the heated area and therewith no mould is formed. As comfortable side effect there is no cleaning of radiators necessary. Additionally, more floor space is available since there is no space required for radiators.
THERMAL COMFORTThermal comfort means the comfort of people in a set room climate. An „acceptable thermal room climate“ is defined under DIN EN ISO 7730 as a surrounding that 80 % of its residents sense as comfortable. In general a room is comfortable if the temperature differences between
- wall surfaces and the ambient air is less than 4 Kelvin
- foot to head level is less than 3 Kelvin
- various wall surfaces (radiation asymmetry) is less than 5 Kelvin
and if the air speeds and their turbulences within closed rooms are small to avoid air draught. Hereby different uses of a room influence the individual temperature requirements.
From experience the following temperatures are comfortable»
- living room» 20 °C to 22 °C
- bed room» 16 °C to 18 °C
- bath room» 24 °C to 26 °C
An underfloor heating is closest to an ideal heating regarding the vertical heat differences. Panel heatings are energy efficient and ideally suited for the use of renewable energies due to their very low flow temperature level. They create a maximum of comfort
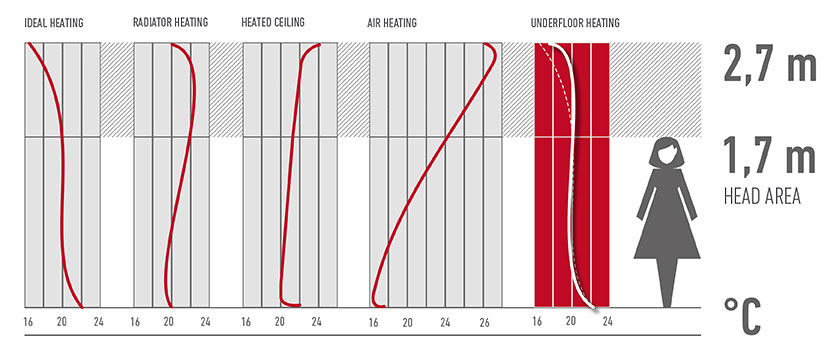
BASIC PRINCIPLE OF COMB PANELSEFFIDUR floor systems WP consist of two preformed steel sheets that are firmly connected to each other to form a honeycomb shaped panel. These comb panels (WP) are fit as floating floor area without connection to the sub-floor, if necessary equipped with pipes and backfilled with screed with a minimum overlap in height of only 5 mm. This way an innovative, highly stable floor system is created, that can be used as floor reinforcement or equipped with pipe for heating or cooling just as required.
comb panels consist of three types»
BASIS without heating |
CLIMATE heating / cooling
|
CLIMATE heating / cooling |
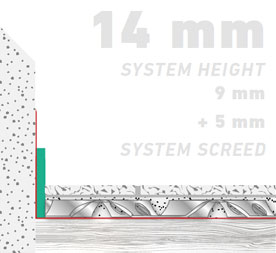
|
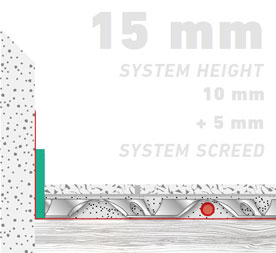
|
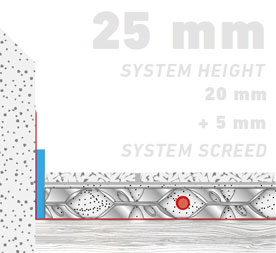
|
system height 9 mm [+ 5 mm SFM] Applicable for reinforcement of the old sub-floor without heating of the new floor. |
system height 10 mm [+ 5 mm SFM] Especially suited for the retrofit of old buildings, where an underfloor heating is only feasible with a low building height. |
system height 20 mm [+ 5 mm SFM] Advantage here» Heating pipes ø 8 mm can be crossed and other media might be integrated. |
ADVANTAGES AT A GLANCELow building height from 9 mm* flush floor finish possible for barrier-free access.
widely independent from sub-floor - unevenness of up to 20 mm can be balanced out without further works.
Reinforcement of sub-floor - highly load-bearing traffic areas feasible.
Excellent controllability - comparable to radiators through fast heat spreading of the steel panel and heating pipe close to the surface this way very short heating-up periods, ideal for temporarily used rooms, fast reaction to external heat input (solar irradiation).
Homogeneous head spreading - low temperature ripple at the floor surface already from a system size of only 15 mm, confirmed through testing according to DIN CERTCO Nr. 7F257.
Highly energy-efficient through low flow temperatures - up to 5 K lower than conventional underfloor heating, i.e. savings on heating costs of up to 10 %
Low material input - this way low static impact on the building through weight of the floor system.
Quickly ready for floor covering already after 5 days, when using system WP1000 heated, system screed SFM with a thickness of 10 mm* and under ideal ambient conditions.
Ideal for modern low temperature heating facilities, condensing boiler technology and heat pumps.
[*without screed overlap flushed for flooring with tiles and flags in middle-bed method, see detailed information at installation instructions under chapter “Backfilling with system screed SFM“.]
system height |
9 mm |
10 mm |
20 mm |
without screed (SFM) overlap and sub- or superstructure |
building height |
14 mm |
15 mm |
25 mm |
comb panel with 5 mm screed (SFM) overlap |
dimensions in mm |
1080 x 480 mm ≈ 0,52 m² |
1080 x 480 mm ≈ 0,52 m² |
1080 x 480 mm ≈ 0,52 m² |
usable area per comb panel |
weight without screed |
5 kg/m² |
5 kg/m² |
5 kg/m² |
one packing unit = 5m² (10 comb panels) |
weight with screed |
ca. 29 kg/m² |
ca. 30 kg/m² |
ca. 45 kg/m² |
comb panel with 5 mm screed (SFM) overlap, at even subfloor |
heat flow density |
- - - |
60 - 90 W/m² |
60 - 90 W/m² |
at a pipe distance of 120 mm and a pipe ø 8 - 10 mm for Θi = 20 °C |
cooling flow density |
- - - |
20 - 40 W/m² |
20 - 40 W/m² |
at a pipe distance of 120 mm and a pipe ø 8 - 10 mm for Θi = 26 °C |
maximum field size without joints |
up to 200 m² for heated areas up to 300 m² for unheated areas |
using system screed SFM |
effidur comb panel in combination with effidur system screed upon separation layer / various insulation |
|
licit traffic loads in kN/m²** |
licit point loads in kN** |
15 mm made of 10 mm WP 1000 with 5 mm system screed SFM overlap, directly borne on reinforced concrete floor |
up to 5,0 |
up to 4,0 |
15 mm made of 10 mm WP 1000 with 5 mm system screed SFM overlap, upon acoustic fleece 4 mm (CP 2) |
up to 2,0 |
up to 2,0 |
25 mm made of 20 mm WP 2000 with 5 mm system screed SFM overlap, upon acoustic panel 25 mm (CP 5) |
up to 2,0 |
up to 1,0 |
25 mm made of 20 mm WP 2000 with 5 mm system screed SFM overlap, upon acoustic fleece 4 mm (CP 2) |
up to 3,0 |
up to 3,0 |
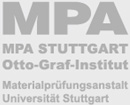 |
35 mm made of 20 mm WP 2000 with 15 mm system screed SFM overlap, upon acoustic fleeces 4 mm (CP 2) |
up to 5,0 |
up to 4,0 |
When avoiding point loads in corner and border areas and subject to the applied insulation material load-bearing capacity of up to 8 kN/m² feasible |
TESTS & CERTIFICATESA large number of tests and certificates prove the compliance of our EFFIDUR floor systems WP with the high demands that are made under the most divers application conditions. Please contact us, we would be glad given you further information individually.
TEST OF FIRE BEHAVIOUR
MFPA Leipzig – Exploratory fire behaviour test analogue to EN 1363-1 and following EN 1364-2
PUSH CONNECTION SYSTEM
IMA Dresden - Tests according to DIN EN 1254-3 and W 534 DVGW
PIPE MATERIAL
SKZ Würzburg, MPA Nordrhein-Westfalen - Test of oxygen permeability according to DIN 4726
SYSTEM SCREED
MPA Stuttgart - Test of bending tensile strength and pressure resistance following DIN 13813
Sächsische Bauprüf Edelmann GmbH - Test of adhesive tensile strength analogue to DIN 1048
LOAD-BEARING BEHAVIOUR
MPA Stuttgart - Test according to European Guideline for Pre-Cast Screed Parts, evaluation according to DIN 1055-3
IMPACT SOUND BEHAVIOUR
ift Schallschutzzentrum Rosenheim - Test according to DIN EN 140-8
HEAT FLOW DENSITY & HEATING-UP BEHAVIOUR
WTP Berlin - Tests according to DIN EN 1264-2/3/4